D & R Flooring
New York Vinyl SPC - Tekapo 6502
New York Vinyl SPC - Tekapo 6502
For SPECIAL prices call us NOW at (604) 532-2211
- 6.5 mm thickness
- 5G Drop Lock
- 30-year residential warranty
- 10-year commercial warranty
New York Vinyl SPC - Tekapo 6502
7.17" Wide x 72" Long, 6.5mm thick (5+1.5). Four-sided bevel edge with a 1.5 mm high-density pad attached, 5G Drop Lock(Suitable for all levels of home). Embossed in register finish. Light Brushed Surface. Matching transitions. 30-year residential warranty, 10-year commercial.
New York Vinyl SPC - Tekapo 6502 is one of the best Vinyl Floors for Houses in Canada. Luxury Vinyl Flooring,
The D&R Flooring and Renovations is located on the Langley Bypass. We stock lots of Vinyl flooring, Laminate flooring, Engineered Hardwood, Moldings, Stair noses, Baseboards, Self Leveling, Underlayment, and more. Throughout February and March of 2024, if you spend a minimum of $2000 for materials, installations, or renovations we will include free delivery for Langley, Surrey, Maple Ridge, Port Coquitlam, and Coquitlam ( BC ). Also if you spend $7000 or more you can get free delivery for Vancouver, Burnaby, Richmond, North Van, West Van, Squamish, Whistler, Abbotsford, Chilliwack, and Mission in British Columbia. D&R Flooring And Renovation - WWW.DRFLOORING.CA
6.5mm Thickness (Wear Layer = 0.5mm or 20mil ) with 1.5 mm high-density IXPE pad attached • 7.17” Wide x 72” Length - Embossed In Register (EIR) Finish • Limited 30 Years Residential / 10 Years Commercial Warranty Stone Product Composite • Floating installation with Valinge 5G Drop lock system can be installed on all levels • 20 mil wear layer durable scratch resistance • 72" ultra-long planks • Embossed in Registered provides the real wood textured finished • 6 Variation in each color • Tolerates conditions from +60°C to -60°C and up to 60 li. ft. without a transition molding • High resistance to direct sunlight • Can be installed on top of water radiant or electric floor heating
Matching Stair Nose, Reducer, and T-Moulding
New York Series SPC vinyl plank specification Specification Standard SPC Flooring Thickness (mm) 5mm Underlayment 1.5mm IXPE STC Rating 73 IIC Rating 72 Wear Layer (mm) 0.5mm CE Certification YES Utilization Class Coating PU Embossing Registered Embossed Bevelled Micro Fiberglass no Click 5G Drop Lock Plank Size 1828.8x182.1mm(72"X7.17") Plank per box 6 Area per Box 1.998 ㎡(21.51 sqft) Density 2000kg/m3
Series
|
|
Colours
|
6501 - 6506
|
Construction
|
SPC
|
Finish
|
Embossed in Register(EIR)
|
Plank Per Box
|
6
|
Width
|
7.17"
|
Length
|
72"
|
Total Thickness (mm)
|
6.5
|
Underlayment
|
1.5mm IXPE
|
Wear Layer (mm)
|
0.5
|
STC Rating
|
73
|
IIC Rating
|
72
|
Density
|
2000KG/m3
|
Sq.Ft Per Box
|
21.51
|
Beveled
|
Mirco - Bevel
|
CE Certification
|
YES
|
Impact Sound Reduction ISO 717-2 30 dB Chemical Resistance EN 423 High Resistance Color Fastness to Light EN 20105-B02 ≥ 6 Slip Resistance DIN 51130 R10 Watertightness EN13553 N/A Wear Resistance EN 660-2 Group T Antimicrobial activity ASTM G 21-96 N/A Fire Rating EN ISO 9239-1 Bfl-S1 Water-resistance 100% Castor Chairs EN425 No Delamination Dimensional stability ISO 23999:2008 X Direction: 0.05% Y Direction: -0.12% Curling ISO 23999:2008 -0.09mm Residual indentation ISO 24343-1:2007 0.01mm Effect of acastor chair ISO 4918:2016 No visible damage Burning cigarette test EN 1399:1997 Method B No visible change Resistance to staining ISO 26987:2008 Index 0: Not affected Migration of Certain Elements EN71-3:1994 + A 1:2000 + AC: 2002 Not Detected CPSIA section 1 08 - Phthalates CPSC-CH- C1001-09.3 Not Detected
NEW YORK SERIES 5G CLICK SPC PLANK INSTALLATION GUIDE General Information Intended for indoor residential and commercial use only, The New York series is suitable for above-grade, on-grade, and below-grade applications. Installations outside these recommendations are NOT warrantable. The New York series is a floating floor and as such, should be allowed to expand and contract freely. It must NOT be glued, nailed, or fastened to the substrate in any way. Install permanent cabinets, vanities, island counters, and similar items first, then fit the New York series around them, leaving a ¼” space for expansion and contraction. For the Best Visual Representation of Your Floor, The New York series uses high variation print technology with embossed register designs for an incredibly natural look and feel. For the best visual effect, open several boxes and “dry lay” the floor before completely laying the floor. Before You Start Perform a pre-install product inspection, examining the flooring’s color, gloss, finish, and quality. Although the New York series has strict quality manufacturing standards on color consistency regardless of Lot Number, it is recommended that the flooring come from the same Lot Number. The lot Number is indicated on the side label of each box. If you are satisfied with your preinstall product inspection, proceed. Storage, Handling Care, and Precautions • Protect carton corners from damage. • Must be stored flat, horizontally, and stacked no more than six cartons high at all times to acclimate cartons thoroughly from top to bottom. • Improper storage can result in warping and difficult assembly. • Storage area and job site should be climate-controlled with temperatures of 20° - 29°C. • Do not install the New York series over carpeting or an underlayment pad. Conditions to Avoid: Avoid installations in sunrooms, solariums, saunas, or any outdoor use. We do not recommend installing this product in rooms that are not temperature-controlled. Avoid long-lasting exposure of flooring to direct sunlight. Extreme solar exposure, heat, and extreme temperature changes can damage the flooring. Subfloor Requirements • All substrates must be structurally sound and free from movement or deflection. • The substrate must be clean, dry, flat, and free of any defects. Carpet staples or glue residue must be removed. • To support the locking system, the subfloor must be flat within 3/16” per 10’ radius. • Smooth and level all irregularities with a (Portland) cement base or synthetic gypsum patching and leveling compound. Concrete • Concrete subfloors shall be properly cured and allowed to dry for a minimum of 90 days before installation. • Always execute the most current version of either the RH Test (ASTM F2170) or Calcium Chloride Test (ASTM F1869) and pH Test (ASTM F710) prior to installation. Results for RH Test should not exceed 85% relative humidity. • Calcium Chloride Moisture Test for the moisture should measure no more than 8 lbs. per 1000 square feet in 24 hours MVER. The pH Tests for alkalinity levels should register between 7 and 9. If moisture levels exceed 85% RH or 8 lbs. per 1000 square feet in 24 hours MVER and /or the alkalinity level is 9 or higher, a moisture barrier must be installed over the concrete. • Prepare concrete substrates in conformance with ASTM F710. New concrete, including lightweight gypsum toppings, should cure for at least 90 days before conducting moisture tests. Wood • Suspended wood subfloors shall have a minimum of 18” of well-ventilated air space clearance above the ground. • Allow wood floors to breathe – do not apply sheet plastic over bare wood floors. • A moisture vapor retarder shall be installed over the crawl space with overlapping widths and lengths. • Wood subfloors must be constructed according to local building codes and be structurally sound with no deflection. • Sand or plane down high spots. Repair squeaky floor prior to installation. • Smooth and level all irregularities with a (Portland) cement base or synthetic gypsum patching and leveling compound. Existing Sheet and Tile Flooring • Existing flooring must be fully adhered to and in good condition. • Existing floating floor must be removed. • Repair any damaged areas. • Heavily cushioned vinyl floor or vinyl floor consisting of multiple layers are not suitable as a subfloor. • Ceramic tile and terrazzo installed must meet flatness requirements. Make smooth by applying a cement overlay, or suitable patching or leveling compound to smooth out surface and grout joints. Radiant Heat • The New York series is suitable for installation over radiant heating systems provided that the heating element is not in direct contact with the flooring. • New heating systems should be running two weeks before installation to remove residual moisture. • Lower temperature of heating system to 60° F for one week prior to installation. • Gradually increase temperature after installation of flooring in increments of 10° F per day to avoid “shock” to the New York series. • Surface temperature should neither exceed nor sustain 29.4°C. Conditioning / Acclimation Acclimate the flooring in unopened box for 48 hours at ideal room temperature range between 20° - 29°C. Conditions in which the floor was acclimated should be maintained for 48 hours pre- and post-installation. Avoid drastic temperature changes as they may cause the New York series to expand and contract excessively resulting in gaps. The best practice is to keep in- service temperatures as close to the temperature at the time of acclimation as possible. Room Preparation • Remove existing shoe molding, quarter round, and doorway transition mouldings. Old or new mouldings must be of sufficient size to cover the ¼” expansion area around the perimeter of the floor. For ¼” expansion spaces that cannot be covered by base moulding, silicone caulking may be used to fill the expansion gap for a more finished appearance. The silicone caulk remains flexible, allowing the floor to continue to expand/contract over the course of its lifetime while preventing dirt from collecting in the gap. • Leave at least ½” between the surface of the flooring and the bottom of electric baseboard heaters to allow circulation. • Undercut door moldings and casings to allow the flooring to fit underneath without restriction. Sweep and/or vacuum substrate to remove all dirt and debris. • After installation, it may be necessary to trim the bottom of any doors to allow for any change in floor height. • Do not fit this floor tight against any fixed, vertical objects (ex. walls, pipes, passageways, staircases). Again, a minimum of ¼” expansion space is required around the perimeter of the room as well as any fixed objects. • All floating floors require that cabinets be installed before installing the new planks. Getting Started • Determine in which direction the planks will be installed. To make the room appear larger or if installing in very small rooms or hallways, it is preferable to lay the planks parallel to the longest room dimension. • Carefully measure the room to determine squareness and to determine the width of the last row of planks. If the width of the last row of planks is less than 2” excluding the tongue, cut and adjust the width of first row of planks accordingly. • Inspect all planks for visible defects and damage before and during installation. Do not install damaged planks. Home’s Pro will NOT accept responsibility for claims on flooring installed with obvious defects. • During installation, inspect the groove area for any debris that may prevent proper assembly of planks. Staggered Layout Prep To begin a staggered layout, the tongue side of the plank shall face the starting wall, groove-side facing outwards. Begin laying planks on the left side of the starting wall, working to the right. For best overall appearance, use either option (a) or (b): a. Start with a full plank for the first row, a 1/2 plank for the second row and a 1/3 plank for the third row. Repeat until completion. b. Start with a full plank for the first row, a 1/2 plank for the second row, and a full plank for the third row. Repeat until completion. NOTE: For rooms larger than 60’ in any direction, a T-Molding is required to account for the normal movement of the floor. When possible, T-moldings should be utilized in areas such as doorways and archways. NOTE: The last row of planks may need to be cut lengthwise to obtain the proper width. The width of the last row shall not be less than 2”. Align a plank that has been cut to the correct length exactly over the first plank in the previous row. Lay a scrap plank over top of the plank to be cut and mark the distance with a pencil. Cut each plank accordingly. When performing this step, remember to allow for proper spacing between the wall and the last row of planks. The First Row Step 1: When assessing the layout for the first row, dry lay all the full-length planks that fit in that row. More than likely, the last plank will need to be cut to complete the row. First, measure the distance between the wall and the surface of the last full plank. Subtract ¼” from this measurement to allow for the spacer. If this measurement is less than 11”, the length of first plank in the row should also be adjusted. This will allow for a longer plank at the end of the row. The first and last plank in each row should be at least 11” in length. With the first row assessed, cut the necessary planks and start by placing ¼” spacers between the short and long side of the planks and the wall. Step 2: Working from left to right, lay the planks in the row by first locking the long side in place, lifting the outside edge and sliding to the previous plank. Fold down and press or tap the end joint downward to lock together. Continue to the end of the first row.
Step 3: The remaining piece cut off from the last plank in the first row will serve as the starter, or first, plank in the second row provided it is at least 11” long. There must be at least 8” between plank end joints on adjacent rows. Second and Consecutive Rows Step 4A: For the First Plank of the second row, position plank with short end-side against the wall and the long side along the first row. Remember to place a ¼” spacer between the wall and the plank. Lock the long edge of the plank by inserting the tongue into the groove at an angle and drop into place (see a). Step 4B: For each Subsequent Plank in a given row, again lock the long edge of the plank by inserting the tongue into the groove at an angle and drop into place (see a). Then repeat Step 2.
NOTE: The lock joints cannot be ‘lifted’ or angled apart when removing or repositioning a plank. To remove a plank, first disengage the top/long angle joint by lifting at a slight angle while pulling the complete rows away from each other. Then simply ‘slide’ the drop joint apart along the floor. Failure to slide this joint apart will damage the drop lock mechanism and prevent proper reinstallation of the affected plank.
Step 5: Use a hammer and a tapping block to tap the long edge of the plank to ensure a tight fit. Any gapping can compromise the locking system. If you do not have a tapping block, you may cut off a scrap piece of floor and use it as a tapping block. When tapping, make sure the scrap piece is locked with the plank you are installing. Step 6: Attach a scrap piece of floor to bridge the gap between ends of planks. Lock and tap until planks are aligned and fully locked. Step 7: Use a hammer and a pull bar to lock the long edges of planks for the final row. Cutting Around Pipes 1. Measure the distance from the wall to the center of the pipe. Mark the plank where the hole for the pipe will be drilled. Remember to allow for the ¼” spacer. 2. Measure the diameter of the pipe. With a utility knife, cut the hole in the plank ¼” larger than the diameter of the pipe. 3. If the hole for the pipe is located in the center of the plank, make a cut perpendicular to the long side of the plank. The cut should be made going directly through the hole. 4. If the hole for the pipe is located near the edge of the plank, make two 45º angle cuts to the hole from the side of the plank closest to the hole. 5. You can now position the two pieces around the pipe. 6. Fill the expansion space around the perimeter of the pipe completely with a high-quality silicone caulking. Finishing the Installation / Floor Care • Remove spacers from perimeter of the room. For tubs, showers, and all wet areas, use a high-quality silicone caulking to fill the expansion space to prevent water seepage under the floor. • Install transition moldings. Do not fasten transitions through the floor. • Install quarter round or baseboard moulding. Moulding must be sufficient size to cover the ¼” expansion space. Do not fasten mouldings through the floor. Fasten into the wall. Again, for any ¼” expansion spaces that cannot be covered by base moulding, silicone caulking may be used to fill the expansion gap for a more finished appearance. • Use plywood, luan, paneling or Masonite when moving furniture or appliances. • Use coasters or proper floor protectors under the legs of furniture. • Home’s pro Rigid core products can be maintained by using a dry Swiffer mop or cleaned with vinyl floor cleaners. Do NOT use abrasive cleaners. • Scratches are site related, and thus, not warrantable. NOTE: Home’s Pro does not warrant installers’ workmanship. Workmanship errors should be addressed to the contractor who installed the floor. Your New York series flooring should be professionally installed by contractors who have demonstrated expertise in installing resilient floors. WARRANTY This guarantee is for replacement or refund of the rigid core SPC flooring and labor as described below. It does not cover costs incurred with loss of time, incidental expenses or any other damage. It does not cover damage from improper installation or maintenance (Including side or end gapping), tears, indentations, stains or reduction in gloss level due to normal use and/or exterior applications. Gapping, shrinkage, squeaks, fading, or structural subfloor-related issues are not covered under this warranty. Temperature variations - excessive heat or below freezing (above 65.6 °C) and (-28.9 °C) – may cause expansion or contraction of the product.
30 Year Residential and 10 Year Commercial Limited Warranty
DR Flooring and Renovations - D&R Renovation
STC/IIC Rating: 73/72
vinyl flooring wholesale
If you want to see more products from the 100% Waterproof SPC Luxury Vinyl Plank New York Series, you can find them in the following list:
Share
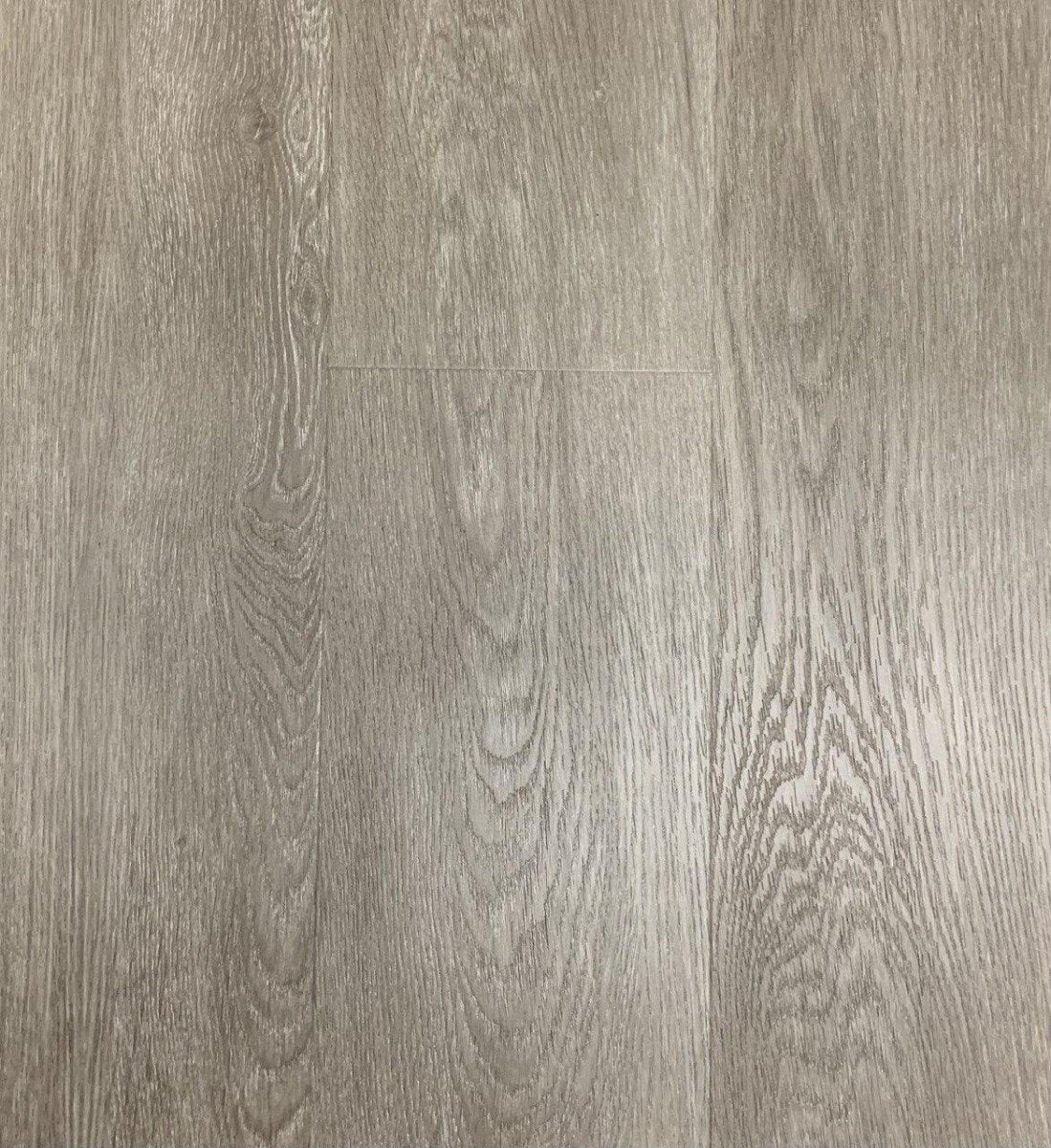
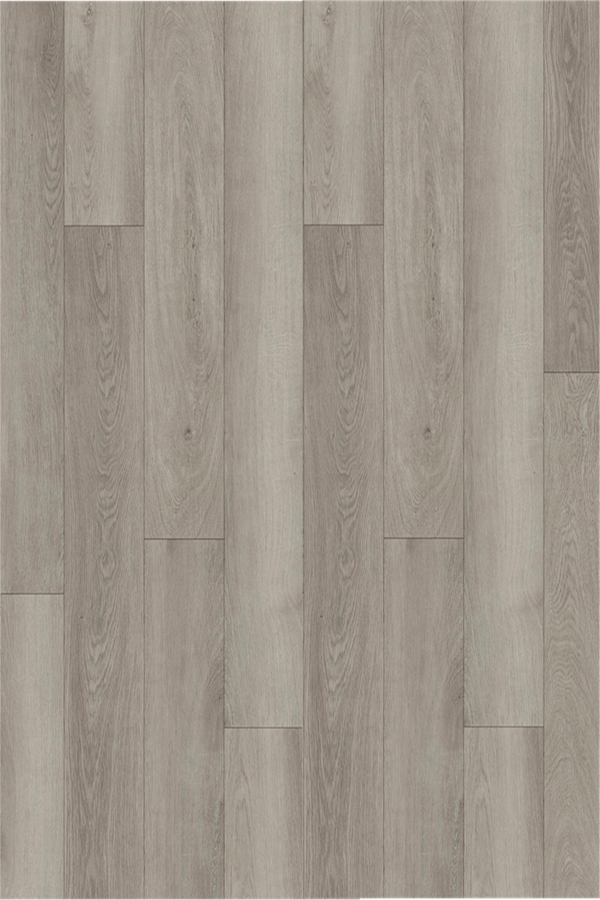
New York Stone Plastic Composite (SPC) Vinyl
Catalogue
Product specification and features available here
Product Spec Sheet
Technical and pack information available here
Installation and Maintenance
Installation and maintenance guidelines available here.
Warranty
The NEW YORK Series SPC VINYL Warranty: This warranty applies to the original purchaser ONLY and is not transferable.
Great service, amazing workmanship and quality, I am very happy with the job done by D&R Flooring also super happy to get free consultation from Hamid, I definitely recommend them.
Subscribe to our emails
Be the first to know about new collections and exclusive offers.